SLA (Stereolithography) printing is another common style of 3D printing where photosensitive resin is cured in layers to create an object.
Unlike FDM printers, SLA printers are loaded with a liquid resin in a vat. The vat is usually sat upon a screen where a laser or other UV light source projects an image onto it. A build plate is lowered to a pre-set distance above the screen (the layer height), causing this thickness of resin to be cured, setting it hard. This cured resin sticks to the build plate due to it being metal rather than the clear plastic vat bottom (known as a FEP).
Layers can be much smaller in SLA printing and can easily handle 0.01mm to 0.1mm layer sizes ensuring it can make highly detailed prints with little to no visible layer lines. SLA printing also builds the model one vertical layer slice at a time meaning the print time is based only on the height of the model and layer thickness.
Most resins are toxic to humans and the environment meaning dealing with resin requires a more advanced setup than FDM. This should include good ventilation to exhaust the fumes, gloves, googles and proper disposal of the any excess. Cured resin is much more safe and uncured resin. After finishing the print it will have to be cleaned, usually with isopropyl alcohol (unless a water soluble resin is used). Supports are also very necessary with SLA printing to ensure that the object is secured to the build plate. These need to be removed after printing and may require sanding. Additionally after the print has been finished and cleaned it requires another short amount of time curing under UV light.
A slicer, like in FDM printing, is also used in SLA printing, but, this creates tens to thousands of layers of black and white images. The white section of the image tells the printer where to fire the UV rays to cure the resin.
Advantages:
Highly detailed prints with little to no layer lines
Can be faster than a FDM printer
Less moving parts to go wrong so can be easier to start printing
Resins can be dyed using photosensitive dye meaning only one base resin is needed for unlimited colours.
Disadvantages:
Toxic fumes and toxic to touch (PPE required)
Need to clean and cure the prints every time
Expensive compared to FDM prints
Not usually as strong as FDM materials
Smaller build sizes than FDM
How does 3D printing work?
FDM (Fused deposition modelling) printing is the process of depositing layers of melted material in a predetermined pattern to create an object.
Normally FDM printers are loaded with spools of thermoplastics, which are fed through a heated block into a nozzle. The melted plastic is deposited onto a heated bed for the first layer before it then builds up. The layers are usually between 0.1mm to 0.4mm but can go lower or higher with more specialist printers and settings. Smaller layer sizes means less visible layer lines and more detail but can dramatically increase the time of the print.
The 3D printer is programmed to follow a script telling it where the nozzle should be, how much plastic needs to be extruded, the temperature and other important settings. This script is normally called GCODE. GCODE is generated by slicer programs which take electronic object files and break it down into a series of lines which the printer nozzle will follow.
Advantages:
Simpler to create larger build surfaces
Wide range of materials in various strengths or flexibilities
Little work to do the print after it has finished (post processing)
Good for prototyping as well as making working mechanisms
Disadvantages:
Lots of moving parts meaning there is often lots of room for errors
Can show layer lines and may need sanding
Overhangs even if supported can be messy
SLA (Stereolithography) printing:
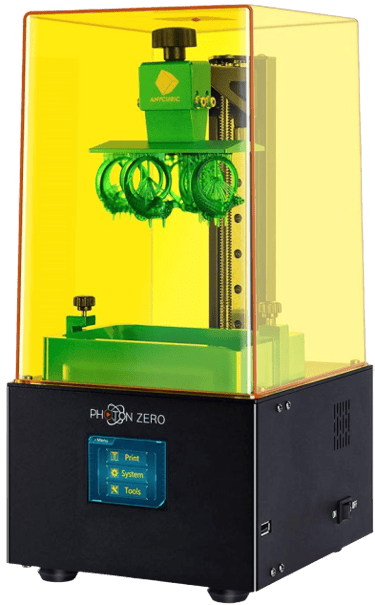
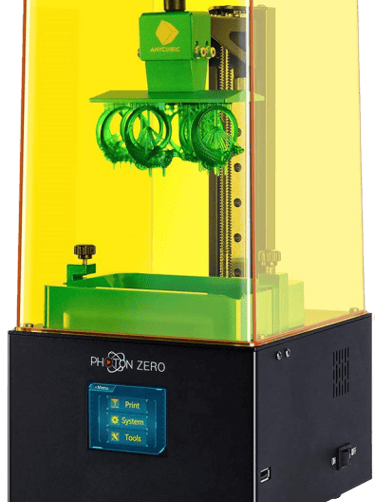
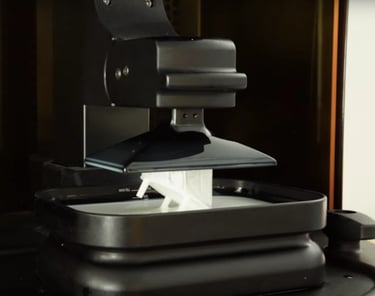
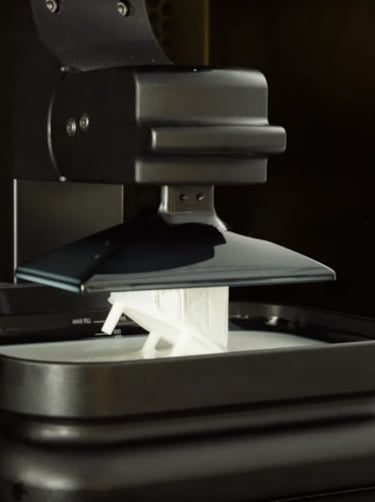
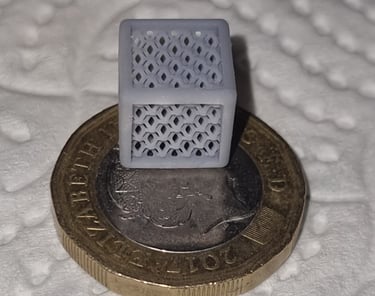
